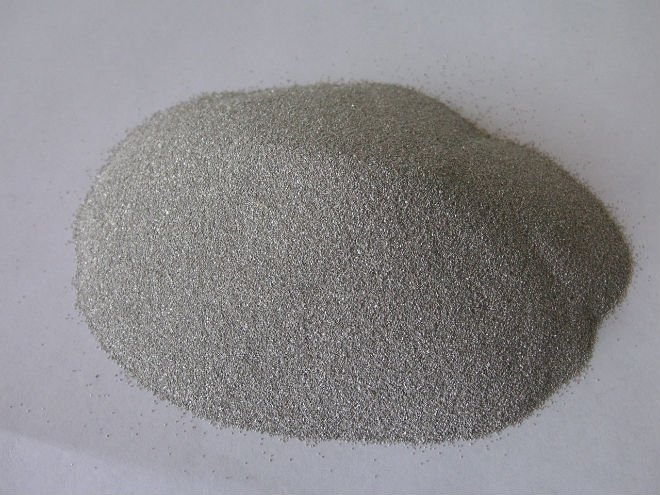
The main methods of producing magnesium powder industrially include the following, each of which is suitable for different application requirements and production scales:
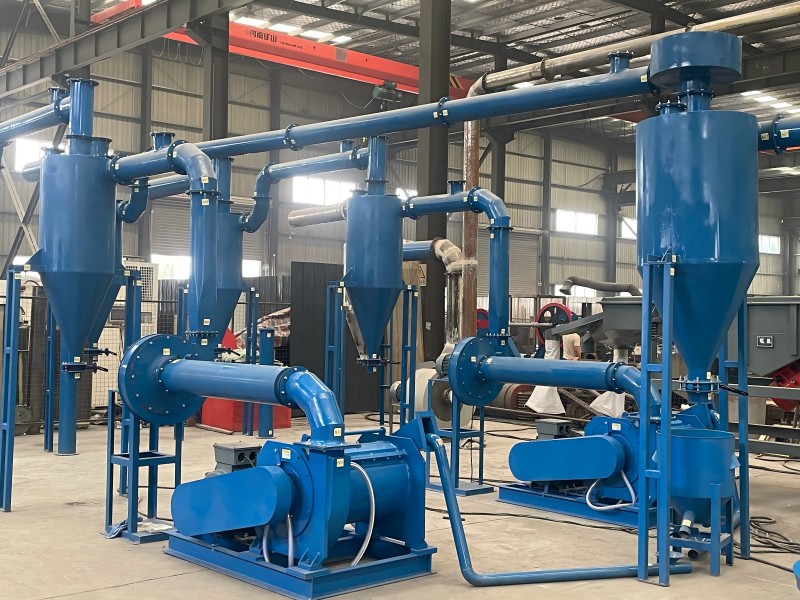
1. Mechanical grinding
• Principle: Physical crushing of magnesium metal blocks by ball mill, vibration mill and other equipment.
• Process: Raw material preparation: cut high purity magnesium ingot into small pieces. Grinding in inert environment: under the protection of nitrogen or argon, the magnesium block is crushed into powder by mechanical force. Grading and screening: Control of powder particle size (usually 50-200 mesh) by vibrating screen or air flow classifier.
• Characteristics: Advantages: low cost, simple equipment, suitable for low and medium purity needs. Disadvantages: irregular particle shape, easy to oxidize, need strict inert gas protection.
• Applications: Fireworks, metallurgical deoxidizers and other scenarios that do not require high purity.
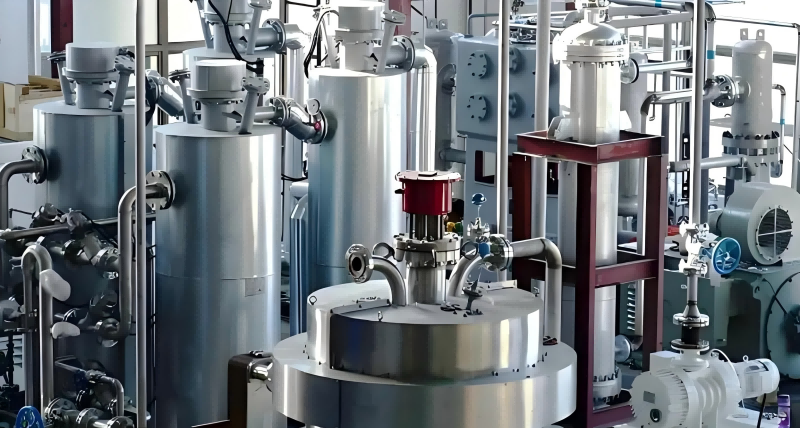
2. Atomization
- Principle: Molten magnesium liquid is atomized into tiny droplets by high-pressure gas (nitrogen, argon), and spherical particles are formed after cooling.
- Process: melting: magnesium ingot in a protective atmosphere melted into liquid state. Atomization: Molten magnesium liquid is sprayed through nozzles and broken into micron-sized droplets by high-pressure gas. Cooling and collection: The droplets are cooled and solidified in a settling tower to obtain spherical magnesium powder.
- Characteristics: Advantages: uniform particles, high degree of sphericity, good fluidity, suitable for 3D printing, powder metallurgy. Disadvantages: large investment in equipment, high energy consumption, need to strictly control the oxygen content (≤ 0.1%).
- Applications: magnesium-based alloy materials for aerospace, high-end manufacturing.
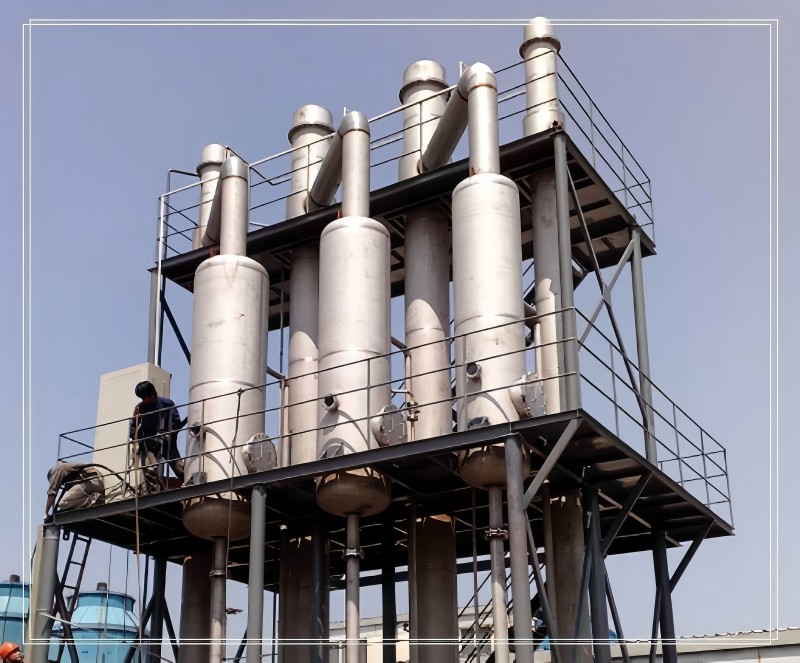
3. Electrolysis
- Principle: Magnesium metal is produced by electrolyzing molten magnesium chloride (MgCl₂) and then processed into powder.
- Process: Electrolysis: Electrolyze MgCl₂ at 700-750℃ to get liquid magnesium. Condensation: Liquid magnesium is cooled to magnesium ingot. Secondary Processing: The magnesium ingot is made into powder by mechanical grinding or atomization method.
- Characteristics: Advantages: suitable for mass production, purity up to 99.9% or more. Disadvantages: long process, high energy consumption, need to support chlorine recovery system.
- Application: High purity magnesium powder demand field (such as medicine, electronic materials).
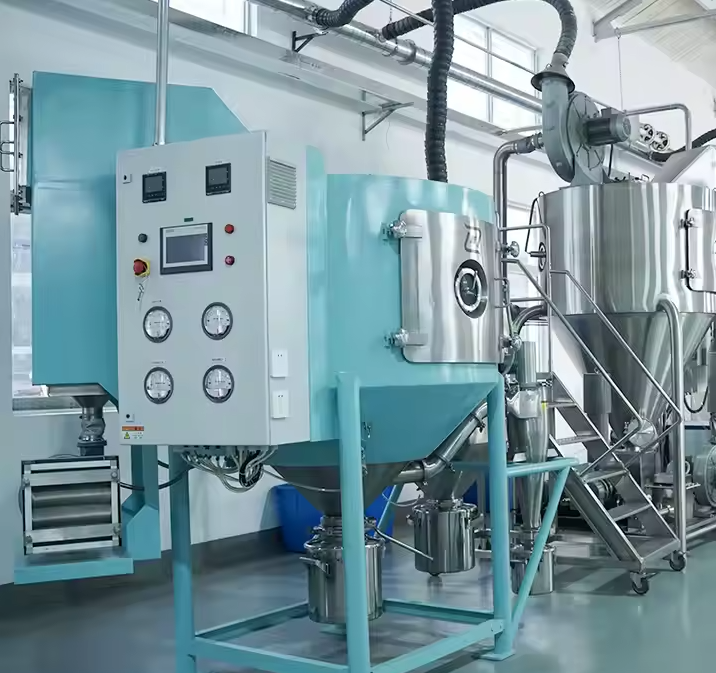
4. Centrifugal atomization
- Principle: Using high-speed rotating disk to centrifugally throw out the molten magnesium liquid, forming fine liquid droplets after cooling.
- Characteristics: Advantages: fine particles (up to nano-scale), uniform distribution. Disadvantages: high technical difficulty, less industrialized application.
- Application: High-end nano-magnesium powder research and development (such as catalysts, energy storage materials).
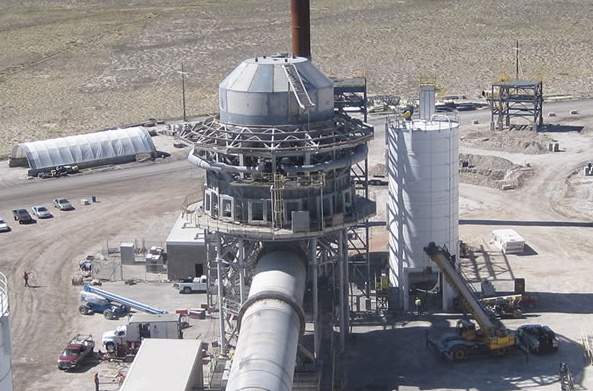
5. Chemical reduction
- Principle: Reduce magnesium oxide (MgO) at high temperature by reducing agent (such as silicon, carbon) to produce magnesium vapor, condense and collect the powder.
- Process: Mixing of raw materials: MgO and reducing agent are mixed proportionally. High-temperature reaction: Heating to 1200-1400℃ in vacuum or inert atmosphere to generate magnesium vapor. Condensation and collection: the vapor is condensed into magnesium powder.
- Characteristics: Advantages: can deal with low-grade magnesium ore, low cost of raw materials. Disadvantages: low purity (usually <99%), high energy consumption.
- Applications: metallurgical additives, chemical raw materials.
Comparison of different methods and selection suggestions
Method | Shape | Purity | Cost | Applicable scope |
---|
mechanical grinding | irregular | 95%-99% | low | fireworks, deoxidizers |
atomization | spherical | 99%-99.9% | high | 3D printing, powder metallurgy |
electrolysis | flaky/irregular | ≥99.9% | medium high | high purity magnesium powder (electronics, medicine) |
centrifugal atomization | spherical/nano | ≥99.5% | extremely high | scientific research, special materials |
chemical reduction | irregular | 90%-98% | medium | metallurgy, chemical additives |
Production Precautions
1. Anti-oxidation: All processes need to be carried out under inert gas (nitrogen, argon) or vacuum environment.
2. Safety protection: magnesium powder is flammable and explosive, it needs to be equipped with explosion-proof equipment and Class D fire extinguishers.
3. Environmental requirements: waste gas (such as chlorine gas) need to be strictly treated, waste residue (such as magnesium slag) can be recycled for building materials.
Summary
- Industrial magnesium powder production methods need to be selected according to the purity requirements, particle shape and cost budget.
- Traditional applications (e.g. fireworks, metallurgy) prioritize mechanical grinding.
- High-end areas (such as aerospace, 3D printing) recommended aerosolization or electrolysis.
- Emerging technologies (such as nano-magnesium powder) can explore centrifugal atomization method, but need to consider the feasibility of industrialization.